红锈的风险评估
金属腐蚀是由于环境引起的金属材料的退化,金属腐蚀导致的直接后果是工程材料使用寿命的缩短,金属腐蚀会导致材料性能退化;金属腐蚀威胁着环境安全,金属腐蚀产物或有腐蚀引发的化学物质的泄露可能严重污染水资源、大气和土壤环境,甚至会引发灾难性的事故。在制药行业,红锈(图1)作为金属腐蚀最主要的直接产物,会直接导致部件的损坏,如管道的渗漏、膜片上附着的红色异物、滤芯上因吸附红锈而导致的堵塞等。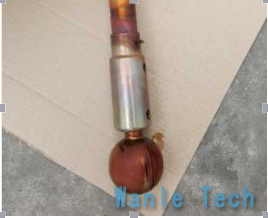
图1 红锈
红锈是一种不锈钢材料上由铁的氧化物或氢氧化物所形成的薄膜,这种红锈也包含铁、铬、镍等元素。锈蚀在生物技术制药行业极为普遍,因为行业中大部分的系统均为316/316L级,且长期工作在高温环境下。红锈现象广泛存在于制药行业各种合金管道中,是一个相对漫长稳定的过程,但是在高温和合金组分变化区域会使此现象更加严重。红锈通常积累在高纯水蒸馏单元、储罐、分配系统(管道、阀门、泵腔及管件等)和工艺容器中。很多制药企业非常关注一些可能存在的累积的颗粒性物质污染产品和无菌系统;如果红锈污染到产品,则产品被视为报废;制药企业无法得知锈蚀的形成速率和沉积速率。当前制药企业除锈和钝化的频率完全依照经验或者规定时间进行,无法做到有效、准确的进行。
对于制药企业来说,对制药系统的除锈和再钝化的频次基于除锈时间间隔或者对系统管路的目视检测来确认。由于目前尚无可用的科学方法用于系统红锈的准确测量,企业的QA人员常根据自身主观的经验来确定系统的除锈再钝化周期。因此,企业SOP就会按照QA做出的合理的风险等级评估,制定基于除锈周期的一年/半年一次或每逢设备停车时进行的除锈和再钝化计划。而这种做法只是药企生硬地完成SOP例行公事,往往并未考虑这种除锈计划是否合适。
近年来,不锈钢管道管件的除锈再钝化维护越来越受到人们的重视。除锈和钝化处理是不同的不锈钢表面处理工艺,但它们又有很多相似的地方。一般情况下,强腐蚀性的化学试剂用以除去金属本体上的红锈,当红锈被去除干净,对金属表面的再钝化方可进行。钝化,可以被认为是一种将不锈钢表面的铁锈、游离铁离子及其他表面污染物去除并使表面形成富铬保护层的特殊清洁工艺。同时,钝化还可大大降低游离铁离子在不锈钢表面形成的几率从而有效抑制铁氧化物(红锈)的形成。磷酸、柠檬酸、硝酸及其他种类的酸性试剂常被用作除锈钝化试剂,而氢氧化钠和氢氧化铵则被用来中和除锈和钝化的酸性废液。中和后的废液通过排污系统排走,在有些情况时,废液也会在现场被废水处理设备处理。当除锈和钝化处理完成后,对系统进行彻底冲洗是非常重要的,只有将除锈钝化过程中产生或引入的污染物彻底排除系统,水系统方可恢复生产,否则,会产生不可预估的严重后果,因为任何一种除锈钝化过程中残留在系统中的化学物质都将明显改变系统的工艺指标。一般来讲,一次典型的除锈与再钝化造成的一个系统停车将持续2到7天,这主要取决于系统循环的个数和整个系统的容量。
红锈在制药用水系统(包括注射水储存与分配系统、纯化水储存与分配系统、纯蒸汽分配系统以及其他洁净流体工艺系统)中的形成属于一种受外界因素干扰驱动的自发现象。总体来说,红锈腐蚀的严重程度主要取决于下述方面:
① 洁净流体工艺系统中管路安装所选用的不锈钢材料的等级;
② 洁净流体工艺系统的安装加工工艺,如焊接、表面抛光和钝化处理等;
③ 洁净流体工艺系统所处的运行环境,如水质和纯度、系统运行化学工艺、运行温度、压力、流速,和其所受到的机械应力和所暴露环境中的氧含量等;
④ 洁净流体工艺系统的维护。
红锈腐蚀产物的形成使不锈钢管道自身质量严重恶化,并在一定程度上大大增加产品质量事故的发生。因此评估制药用水系统中红锈的存在对生产工艺及系统长时间运行的潜在风险显得尤为必要。导致制药用水系统中红锈形成的各种变量因素可分为以下三类:
① 第一种变量因素对红锈形成影响较小。此类因素为表1和表2中各种变量因素对红锈形成的机制提供理论依据。
② 第二种变量因素对红锈形成具有较大影响。此类变量因素有一定的经验数据收集作为支持,应纳入洁净管道施工工艺设计的考虑范围中。
③ 第三种变量因素对红锈形成具有很大影响。此类变量因素有相当成熟完善的业内经验数据作为支持,须纳入洁净管道施工工艺的考虑范围中。
新建制药用水系统安装阶段,用户应选择资质齐全,施工水平高,业界口碑好的正规安装供应商,并要求供应商应按照相关要求对系统管道管件及零部件的材料进行选购,用户应亲自或委托第三方对所选购材料的材质、元素构成等指标进行定量检测验收。对于不同工艺需求的制药流体系统,供应商应根据相关要求选择机械抛光或电抛光的不锈钢管道完成安装工作。安装过程中,供应商应安排焊接水平优秀的焊工及其团队对管道进行配置定位和安装,焊接作业时应根据管道材质和现场环境选择适当的焊接工艺和参数,严格把控充气保护时间和用量。焊接质量对于系统在运行周期中的红锈现象也具有直接的影响,焊接时的电流参数、充气时间如果设定的不恰当,将导致焊道焊偏、未融合、回火色重等焊接质量问题,这些问题如果不能及时发现并整改,焊道区域在运行周期中将首先出现红锈腐蚀现象;如果在焊接过程中出现焊道氧化现象并未能将氧化焊道从系统中切除,焊道将以铁氧化物(红锈)的形式进入系统中,这意味着系统尚未开始运行,就已经出现红锈现象了,焊道氧化是对不锈钢管道材质等级不可逆的损伤,这种焊接质量事故在洁净管道系统安装工程中是不被接受的。安装工作结束后,应及时对新系统进行清洗和酸洗钝化处理,并将处理过程记录在竣工文件中归档。对于已有制药用水系统的改造项目,除在新增加管道的安装过程应根据上述要求进行施工外,供应商还应对旧系统内部的红锈腐蚀状况进行评估,并进行相应的除锈钝化处理。
影响因素 | 注释 |
种类3(影响程度高) | |
材料选择 | 材料选择的合理(如316L不锈钢)与否在于所选材料在使用环境中的抗腐蚀性。如:低碳钢与高碳钢相比抗腐蚀性更加。合理的材料选择可抑制早期或已开始加速的腐蚀。提高镍元素的含量将有效增强不锈钢的抗腐蚀性。 |
机械抛光 | 冷加工技术在金属表面留下的纹路中可能残留抛光残余颗粒。表面抛光的不均匀性所导致的表面以下内部面积的累计增加会使材料更易被腐蚀。 |
电抛光 | 可减少材料本身直接暴露在氧化性流体或氯化物中的接触面积,同时可减少各种机制(如卤化物腐蚀、热应力腐蚀等)导致的微点蚀的形成。表面吸入点也将随表面光洁度的提升而减少。 |
钝化 | 可有效抑制不锈钢表面腐蚀的发展。钝化方法的效能包括钝化深度和表面金属元素的优化分布(如铬铁比)将决定金属钝化后的抗腐蚀性和腐蚀速率。 |
金属元素构成 | 主要是钼、铬、镍等。金属微观结构的性能影响晶界杂质的沉淀。这些杂质向表面的迁移将加剧腐蚀源有表面向内的腐蚀。不同的焊接接头所含的硫含量由于焊池变化可能导致焊口不能焊透,此处极有可能成为初始腐蚀点。 |
焊接工艺、参数及充气方式 | 不当的焊接方法有可能导致铬在热影响区的流失从而降低金属的抗腐蚀性能。焊接时的不连续性将为熔滴渗入杂质提供机会。不良焊口中产生的裂纹可能使钝化膜上和活跃的腐蚀源周围出现缺口。合理的充气方式可有效防止回火色氧化膜导致的焊接污染及与之相伴生的抗腐蚀性损伤。钝化作用不能逆转由于充气不当造成的不良结果。 |
产品类型和加工方法 | 成型工艺显著影响最终铁素体的含量(如锻件中铁素体含量远低于铸件)。锻件表面锻压纹的空隙会增加金属形成微点从而形成点腐蚀的风险。缩小硫含量的差异将提高优良焊接的成功几率。 |
类型2(影响程度较高) | |
安装环境 | 碳钢腐蚀、划伤、暴露在化学环境中、管路中冷凝物或液体的留滞等可能造成不确定的腐蚀现象应在钝化前施以除锈步骤。如不对安装环境可能造成的腐蚀加以重视,会影响最终的钝化效果。 |
系统的改造和扩展 | 在新运行的系统中氧化物会以不同于旧系统的速率形成,并在初始阶段形成可迁移的1类红锈。由于氧化膜的存在,旧系统具有更稳定的化学稳定性,只产生少量的氧化铁或氧化铬。而新系统中会产生新的1类红锈并分布在整个系统中,故腐蚀起因很难确认。 |
制药用水系统运行过程中,存在大量的可能导致红锈滋生或迅速蔓延的高风险因素。如配液系统中的腐蚀性工艺流体,尤其是当流体介质中含有氯,极易对系统不锈钢管道表面造成点腐蚀,生成并加速红锈的发展。更加普遍的红锈滋生风险体现在流体工艺系统的运行参数设定,如流速、运行温度、运行压力等常规运行参数。一些科学机构发现,流体流速过高时,其含有的腐蚀性因子(包括高纯度水)会对不锈钢表面钝化膜造成侵蚀破坏,这一现象在循环流体工艺系统离心泵泵腔内部和叶轮表面尤其突出;系统运行温度将直接决定红锈产物的类型,注射水系统中Ⅱ类红锈与纯蒸汽系统中的Ⅲ类红锈就是因其各自所处氧化环境中温度的差异而在形成机制上有所不同的;系统压力存在的不稳定梯度分布会导致纯蒸汽系统中冷凝水的残留,为系统内部滋生红锈和微生物都提供了温床。此外,系统在线清洗(CIP)和在线灭菌(SIP)的工艺、系统维护的周期和具体内容以及除锈钝化处理的频率和除锈钝化试剂工艺参数都会对系统运行过程中红锈的滋生和发展产生不同程度的促进影响。
影响因素 | 注释 |
|
类型3(影响程度高) |
|
|
腐蚀性工艺流体 | 腐蚀电池一般在钝化膜的缺口中形成,如氯腐蚀电池,可逐渐加速腐蚀机制。此类情况对诸如高盐缓冲液罐的影响极大。 |
|
高剪切/高流速环境 (泵轮、喷淋球、三通等) |
腐蚀性因子可消耗或侵蚀钝化膜,进而将基质金属组分颗粒暴露在运行系统中。比较严重的例子如在泵轮尖端形成的点腐蚀,或者流体腐蚀管壁形成的腐蚀点。在纯蒸汽系统中,高流速部分可有效吹洗管壁使该部分管壁避免氧化铁等污物的持续积累并将氧化碎块带入下游,成为下游管路被腐蚀的潜在风险。 |
|
运行温度及温度梯度 | 系统运行温度及温度梯度影响最终铁氧化物的类型(Ⅰ、Ⅱ、Ⅲ型红锈)、易除性、趋稳性、氧化物的稳定性或迁移性等。除锈钝化效果很大程度取决于系统运行温度。如在已形成黑色氧化铁(Ⅲ型红锈)的纯蒸汽系统中应在钝化之前进行除锈处理。多种光谱分析法可确定这些杂质种类。 |
|
气相组分(包含溶解气体) | 对于注射水和纯蒸汽系统,在指定的电导率和TOC指标及有钝化膜存在前提下,溶解气体组分对红锈形成仅有有限影响。杂质在蒸馏及汽化过程中有可能随溶解气体组分发生迁移。 |
|
使用工艺参数,工艺介质,使用频次 |
氧化物种类,腐蚀风险,除锈方法及红锈形成时间很大程度上被运行参数(温度、工艺)影响。SIP、流速、温度及密封可能会影响红锈沉积的形成种类和位置。 合理的设计可帮助系统减少上述不利影响。而不良密封常使系统处于压力梯度中,从而将腐蚀产物通过蒸汽冷凝引入系统中。高盐缓冲罐的长时间运行和搅拌作用可加速腐蚀的发生。伴随设计不合理的CIP进行的SIP将增加腐蚀发生的几率并增大后续除锈钝化处理的难度。 |
|
系统CIP及清洗方法的选用 | 将系统暴露在CIP循环下,以及专业化学清洗试剂会很大程度上影响红锈出现的风险。系统中与CIP接触的部分会减少形成或聚集红锈的可能。CIP系统试剂配方中是否有酸或热酸是影响红秀生成的一个重要因素。CIP进程中酸洗过程及过程温度是非常重要的。如:使用始终浓度(2%-20%)的磷酸循环清洗可维护复原钝化膜。 |
|
氧化还原电势 | 使用臭氧对纯化水或注射水消毒对抑制腐蚀发生也起到有力作用。 |
|
类型2(影响程度较高) |
|
|
系统维保 | 系统组件如磨损的蒸汽调节阀体、错位的垫片、破损的阀膜片和泵轮叶片以及被腐蚀的热交换器管道等都被认为是1类红锈的滋生的温床。 | |
滞流区域 |
流动的氧化性流体可以保护钝化膜。(研究认为注射水储罐的氮气保护层对钝化膜有消极作用,因为氮气的存在抑制了流体中的氧气含量。) 不能迅速从蒸汽管道中被排除或因阀门不当次序而存留的冷凝液可能会聚集运送管道氧化产物或含有可溶于蒸汽的物质。这些物质会凝聚在系统某些分支终端如喷淋球、液位探测管等。这些氧化沉积物常为轻附表面的氧化铁。虽然其较易除去,但在较大管路仍较难清除且有碍视觉清洁。 |
|
压力梯度 | 此情况仅在纯蒸汽系统中出现。分配系统中的压力变化会影响冷凝水量和蒸汽质量。如果系统中各部分处在不同压力范围,冷凝水将不能在水平截面被有效除去,继而其会在较高压力环境下重新汽化,从而降低蒸汽质量,并且将蒸汽冷凝水中的杂质带入蒸汽中。 | |
系统寿命 | 取决于系统维护状况,主要包括除锈和钝化的频次,CIP处理及稳定钝化膜的形成。与旧系统相比,研究发现新系统会产生与年限不成比例规模的1类红锈。纯蒸汽系统中,尽管氧化层随着年限推移而逐渐稳定,但他们在逐渐变厚的同时也会在高流速部分发生氧化层颗粒脱落的现象。系统使用时间的延长对红锈的形成有利有弊,因此针对初始腐蚀判定的常规系统监测显得尤为重要。 |
为降低制药流体工艺系统产生红锈的风险,企业需采用“质量源于设计”的管理理念,从设计源头开始进行有效控制,更为详细的内容可参见笔者主编的《制药用水系统(第二版)》第9章与第10章相关内容。
参考文献
1. FORCE Technology:Rouging of Stainless Steel in WFI Systems Examples and Present Understanding,2007:11
2. PHARMACEUTICAL ENGINEERING:Online Rouge Monitoring,A Science-Based Technology to Measure Rouge Rates,2011:18
3. The American Society of Mechanical Engineers. ASME BPE,2012: 15.
4. STERIS LABORATORY REPORT #3217:LABORATORY DEROUGING OF SIMULATED ROUGE USING CIP 200,1999:8/99
5. STERIS LABORATORY REPORT #3228:THE EFFECT OF CIP 200@ ON PASSIVATION OF 316 STAINLESS STEEL,1999:7/99